Young Canadian Watchmaker Bradley Taylor And His First Watch, the Paragon
In conversation with an unusual watchmaker, from a country that isn’t really known for watches.

Earlier this year, we shared a story on a young Canadian watchmaker by the name of Bradley Taylor and the result of his first solo project, the Paragon. Selling out all of the 12 pieces in about two months can be considered quite an achievement by a start-up brand. Reason for us to sit down with Bradley Taylor once more and talk about what it took to create this watch, what the philosophy behind it is, how ‘Canadian’ the watch is and his consideration of doing something in-house or not.
The Paragon is the first-ever watch created under his own name, but Bradley Taylor has experience with building a brand and creating a watch design from the ground up before. We briefly touched upon the subject in our previous coverage, but joining forces with a fellow-Canadian classmate during his education in Le Locle, Switzerland, he started out as the ‘Taylor’ in Birchall & Taylor. Based out of Toronto, Charles Birchall and himself set out to create a luxury watch brand, basically the first of its kind in Canada and tried to offer something fresh to discerning collectors. Sadly, it didn’t turn out to have a happy ending.
Today, we’ll talk to Bradley Taylor as he shares his background, his experiences in the industry and with his former partner and explains more about his Paragon watch.
Robin Nooij, MONOCHROME – Bradley, you’ve explained your path to get to creating your own brand and launching your first collection, the Paragon. How did that come about?
Bradley Taylor – Well, it all started when I bought my first watch, which was nothing special but got me hooked on watches quite rapidly. I opened it up after getting my first set of tools, worked on it, and eventually destroyed it I think. From there on out I know I wanted to do something in watchmaking. I got the chance to go to watchmaking school at the Korpela & Hofs Watchmaking Competence Centre in le Locle. A huge step but I loved it all the way. During my education, I had the chance to meet some of the industry legends, like Mr Dufour, who have inspired me ever since.
You finished school in three years and went to Patek Phillipe. Not the smallest of companies in the industry. How was that experience?
Yes, I worked in after-service for Patek and Hublot for a while and while it thought me a lot, it also taught me what I didn’t want to do in the industry. During my years studying watchmaking, I became really close friends with Charles Birchall, a fellow student and Canadian too. Our bond became very tight and we stayed in touch even when apart due to our personal career plans. He worked with Roger Smith for instance, in the UK, while I stayed in Switzerland. After we both ended up back in Toronto we quickly drew plans for our own company and our first watch. That all led to the Reference 1 which we launched in 2018. We wanted to design and assemble our own watch, but with respect to traditional watchmaking.
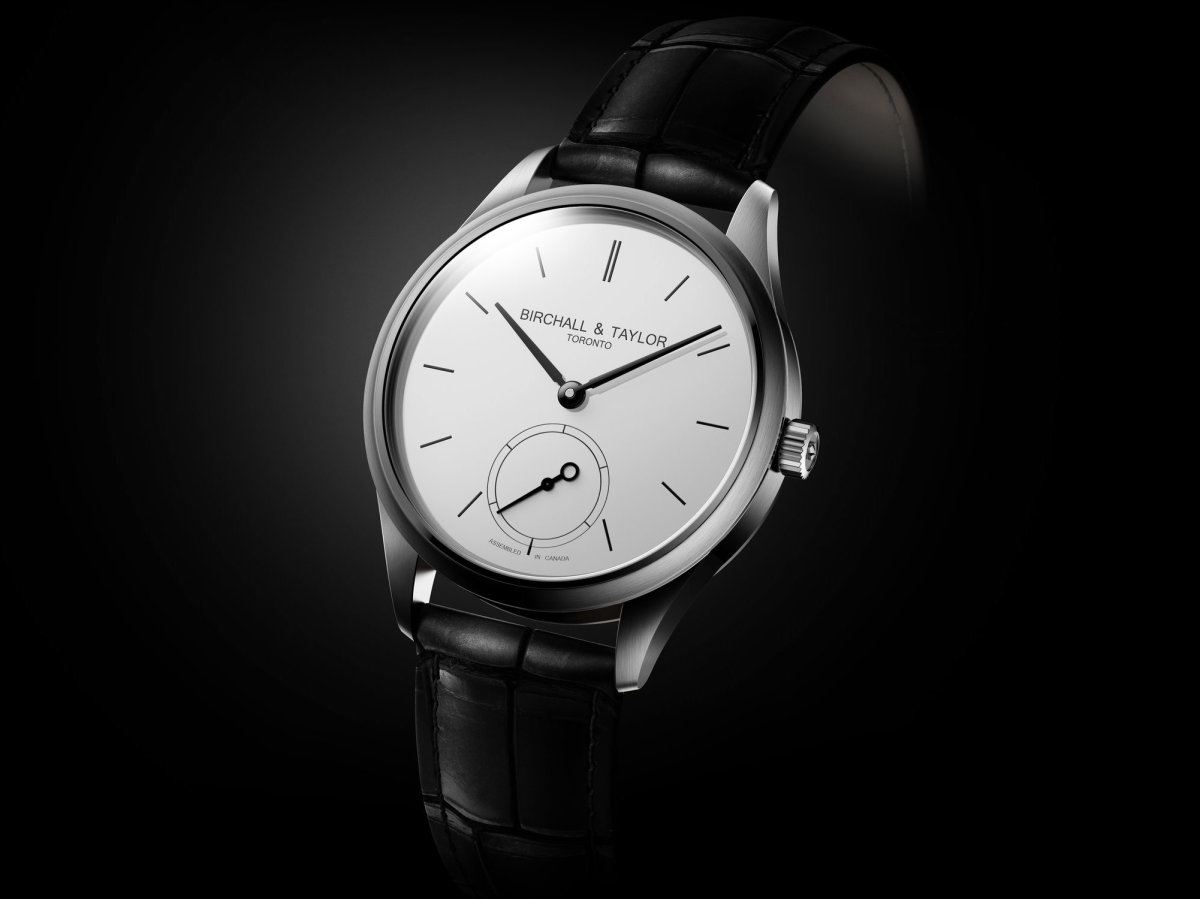
The Birchall & Taylor Reference 1 had a promising start but it wasn’t meant to be in the long run. Can you explain to us what happened?
We started off strong in 2017, with some nice feedback and a good amount of orders so we were really happy. It went so well that we decided to move to a larger workshop in late 2019. We found a place, set up shop, were looking to expand the team and get things going again. But Covid lost us more than half our orders. That hit hard and as we were still making investments in our company, it couldn’t have been worse possible timing. We tried our best to keep things going but it proved too much.
When we had to shut down the workshop It was hard to stay motivated, I even stopped working on watches altogether and didn’t touch my tools for a month or two. But eventually, I picked them up again and I realized it is what I love doing the most. I talked to Charles and we agreed that I would take the concept of our next watch and continue developing it, which would eventually become the Paragon.

So could you tell us more about your watch? What’s the idea behind it?
In all honesty, I just want to make the best watch I can ever think of. Every part I design is made by the best possible manufacturer. These are complemented with parts made by me when I can’t find the right suppliers for a part. That was what I ran into with the hands, after approaching many specialized hand manufacturers no one could make what I wanted, so I developed a process to make them myself.
Some people don’t understand it and only focus on in-house. To me, that is irrelevant, as quality at the end of the day is most important. Take the dial for instance, which is made by Comblemine, Kari Voutilainen’s dial factory. To me, they make the absolute best dials in the world. They helped me execute a dial that is a fresh take on guilloche.
I have never seen a watch with guilloche just on the outer edge of the dial and I thought it would look rather unique. The decision to reverse the pattern in the small seconds subdial is to create some sort of movement on the dial.
Those purple hands, could you explain to us and our readers what makes them so special that most specialized hand companies can’t make them?
First I use a special steel from Japan, that has virtually no imperfections in it. It bothers me to spend hours polishing a hand only to find a tiny flaw in the steel itself which means I must throw it away immediately. The steel I now use doesn’t have that issue.
I spend up to 20 hours on a good day, making just one hand. It starts off with a laser-cut blank which I then shape into the final shape by hand. I then polish them to a mirror finish and flame-color them. I wanted to make purple as that stands out more and is a lot more difficult to do. The bandwidth for the perfect purple colour is a lot narrower than getting a perfect blue. And each hand can take up to 5 or 6 attempts before I think it is perfect. That means I have to polish off the oxidation and start over with the tempering.
There’s also a fair amount of ‘Canada’ in your watches. Could you elaborate on that?
I wanted my watch to reflect the best our country has to offer, both in watchmaking and other elements. The font I used is designed by Canada’s foremost typographer, Ian Brignell, who also worked on the famous Paramount lettering.
What I looked for in determining the right font for my hour numerals was a design that tied them all in together. If you put two random numerals together, they must appear from the same family.
I also use squared head screws for the caseback, something that might sound rather odd to some but has a history in Canada too. It was originally invented by a Canadian by the name of P.L. Robertson and was the first alternative to flathead screws. The square hole prevents any slippage and potentially damaging something. I believe mine are the smallest in the world at only .65mm square. They are machined for me in a rough shape, and I finish them by hand. It’s just another Canadian element in the watch.
I understand you offer bespoke options to a client. Are there any limitations?
On the Paragon the hand temper colour and dial colour are chosen. Of course, I work with each client and make sure that balance and legibility are maintained.
In the future, I will be working with clients on special projects where there will be more possibilities for bespoke work. For now, though, the focus is on delivering the first 12 pieces to their owners.
For more details, please visit Bradley Taylor’s website.